Virtual Online Sessions Lean Six Sigma Yellow Belt Skills Training
Classes are full - Registration is closed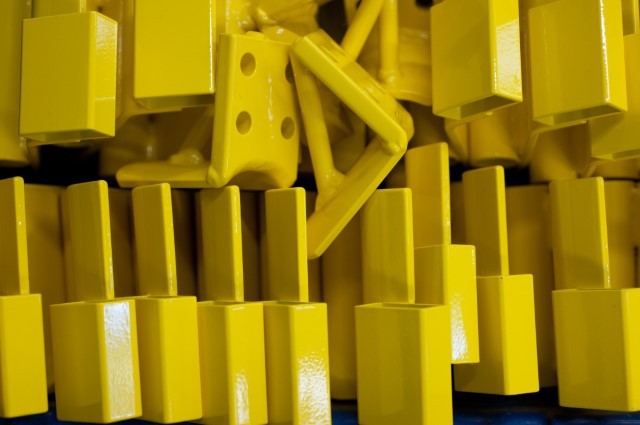
Description:
The Six Sigma Yellow Belt skills training is a 12-hour training program providing an overall insight into the techniques of Six Sigma, its metrics, and basic improvement methodologies.
Learning Objectives:
The Lean Six Sigma Yellow Belt develops team understanding and effectiveness in supporting Six Sigma projects throughout a facility. The program builds day-to-day workplace activities resulting in reduction of cycle times, improved quality, and less waste.
Yellow Belt Covers the Following Topics:
• What is Lean Six Sigma?
• Understanding and Developing the SIPOC Diagram
• Process Mapping (the 6-foot view)
• C&E Matrix
• Failure Modes and Effects Analysis
• Basic Statistics
• Data Analysis, Tools and Graphing
• Controlling the Process
Who is this training for?
Format:
DMAIC Process:
Schedule:
THURSDAYS, 12:00 noon – 2:00 p.m. - SESSION FULL
Sept 8 to October 13, 2022
FRIDAYS, 9:00 a.m.-11:00 am. CT. - SESSION FULL
Sept 9-Oct 14, 2022
Fee:
$750 per person. Includes all training materials.
Two participants are required from each company to work together on out-of-class projects/assignments.
Registrations are non-refundable, and must be paid prior to start of class.
The Instructors

Kate Chepeleff
Classroom Leader and Project Coach
CITEC Business Solutions
Kate Chepeleff is a project/process engineer with more than 20 years of engineering experience in heavy industry and manufacturing with leading companies including Corning and Alcoa. She is a certified Lean Green Belt and Six Sigma Black Belt with strong communication skills applied across many levels of an organization. She is recognized for her leadership on transformational team-based initiatives, continuous improvement expertise, and as a results-driven change agent. Kate has a solid background in training program development and delivery.
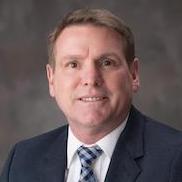
Brad Blair
Industrial Liason Officer, Nebraska MEP
Brad has 25 years of Manufacturing Engineering and QA Manager Experience along with a Bachelor’s Degree in Industrial Technology.
As a Manufacturing Engineer Brad led and participated in many LEAN initiatives including Value Stream Mapping/Current and Future State Projects/Root Cause Analysis utilizing Six Sigma Green Belt methods. Employing CAD software(’s) Brad designed Jigs and Fixtures for Quick Change and Poka Yoke solutions along with Plant layout for flow and efficiency.
Brad believes in Employing a principal of “Attacking the Process and not the Individual” while encouraging Employee participation for a more comprehensive outcome.